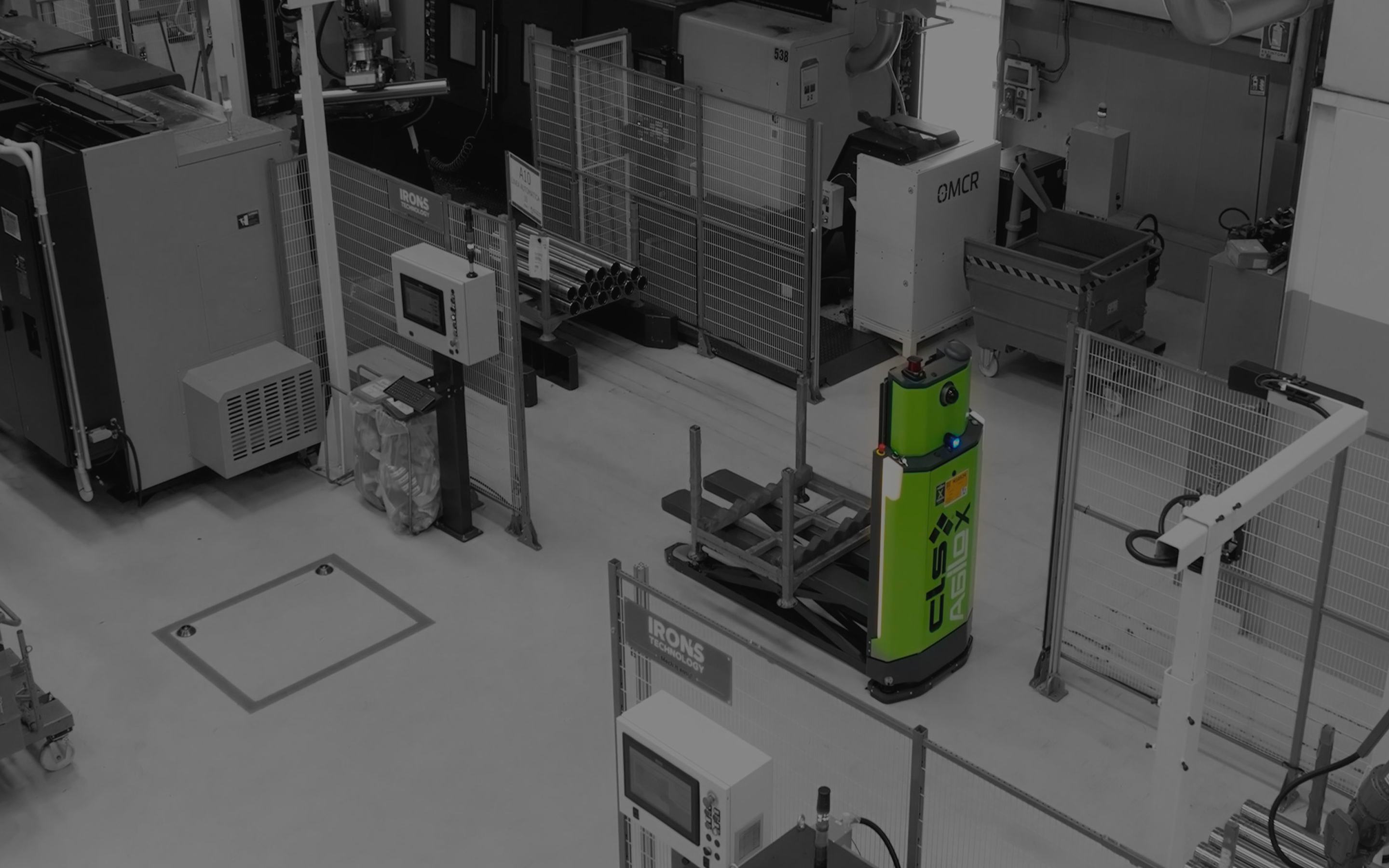
INTERPUMP HYDRAULICS
HOE INTERPUMP HYDRAULICS
PRODUCTIE HEEFT GEOPTIMALISEERD MET DYMATION.
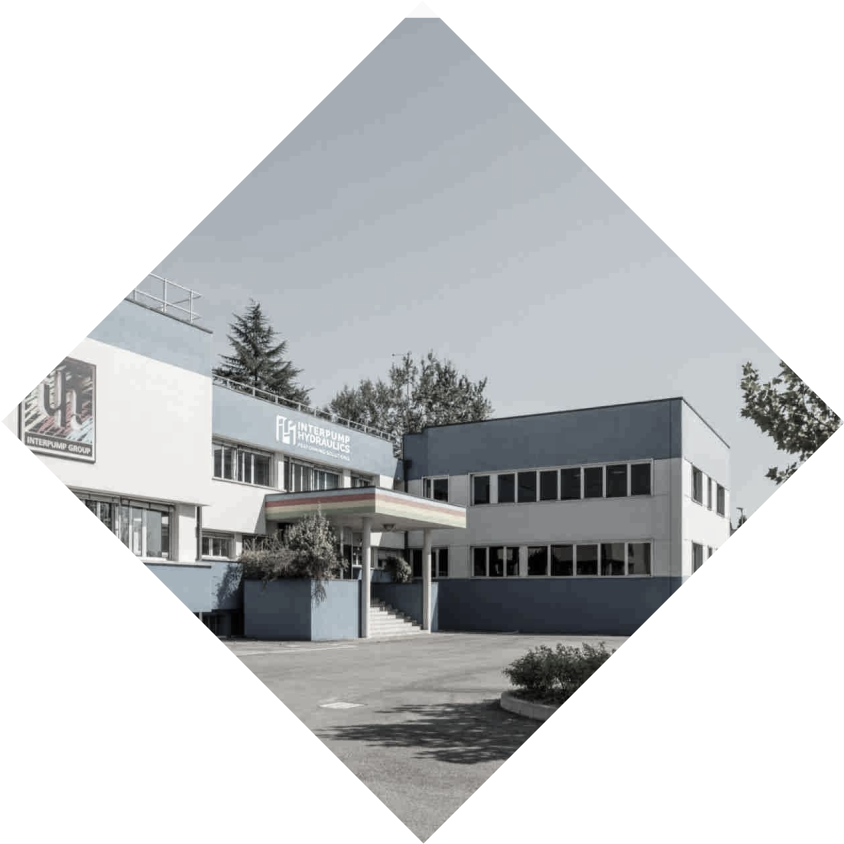
KLANTINTRODUCTIE
Interpump is een toonaangevend bedrijf in de productie van telescopische cilinders.
Interpump is een toonaangevend bedrijf in de productie van telescopische cilinders, met een productielocatie in Faenza. Het assortiment omvat voorcilinders, dubbelwerkende telescopische cilinders, lichte cilinders en onderbouwcilinders. De lancering van de nieuwe voorcilinder Serie 5 vereiste een verhoging van de productiecapaciteit, wat het bedrijf ertoe bracht te investeren in een nieuw geautomatiseerd draaisysteem. Dankzij de samenwerking met Dymation, Yaskawa en Iron’s Technology werd een innovatief systeem ontwikkeld voor de productie van deze nieuwe oplossing.
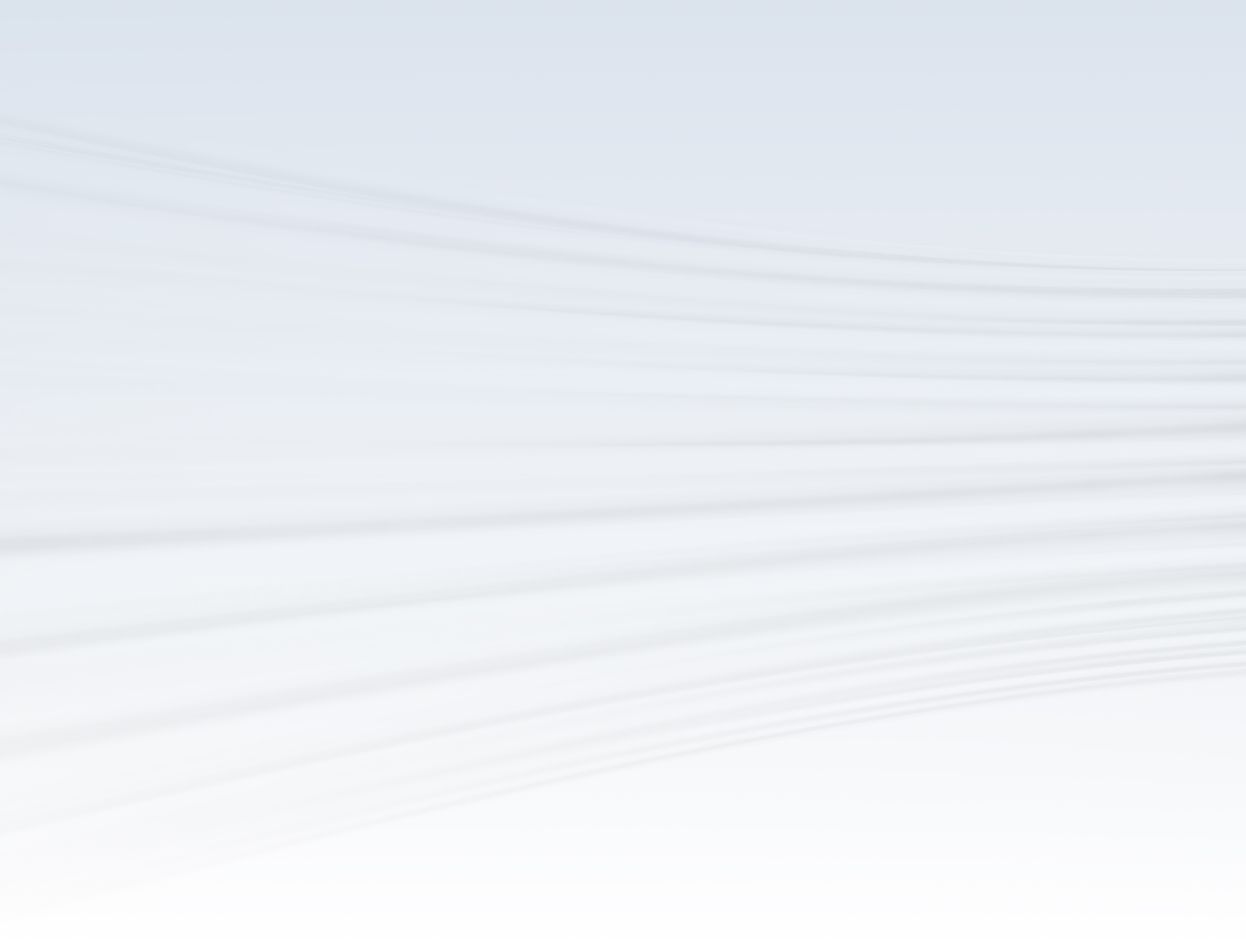
Het bedrijf stond voor een aanzienlijke uitdaging: het vergroten van de productiecapaciteit om aan de groeiende vraag naar de nieuwe Serie 5 voorcilinder te voldoen, zonder concessies te doen aan efficiëntie en kwaliteit. Het doel was het implementeren van een geautomatiseerd systeem om de workflow te verbeteren, continue monitoring van de productie mogelijk te maken en menselijke middelen optimaal in te zetten, terwijl hoge veiligheids- en betrouwbaarheidsnormen gehandhaafd bleven. Om deze resultaten te bereiken moest Interpump echter verschillende problemen overwinnen:
- Noodzaak om de productiecapaciteit te verhogen
- Automatisering van de workflow
- Monitoring en bediening op afstand
- Veiligheid en betrouwbaarheid
- Optimalisatie van menselijke middelen
Dymation heeft een geavanceerd automatiseringssysteem geïmplementeerd gebaseerd op een Autonomous Mobile Robot (AMR), verbonden met vier industriële robots via speciale beheersoftware. Dit systeem:
- Verhoogde productiecapaciteit: Dankzij automatisering heeft het bedrijf het productievolume verhoogd zonder uitbreiding van het personeelsbestand.
- Verbeterde kwaliteitscontrole: Het geautomatiseerde systeem zorgt voor een superieure precisie bij assemblage en kwaliteitscontroles, waardoor afval en herbewerking worden verminderd.
- Lagere operationele kosten: Door procesoptimalisatie zijn de productiekosten verlaagd, waardoor de winstgevendheid van het bedrijf is verhoogd.
- Betere inzet van personeel: Operatoren, bevrijd van handmatige taken, werden toegewezen aan strategisch waardevollere functies.
- Veiligheid en betrouwbaarheid: De aangepaste AMR verbeterde het transport van zware lasten, verminderde het risico op ongelukken en verbeterde de werkomstandigheden.
Dankzij deze behaalde resultaten heeft het bedrijf besloten het systeem uit te breiden naar andere werkstations, waarmee het zijn toewijding aan voortdurende innovatie en procesverbetering verder versterkt.
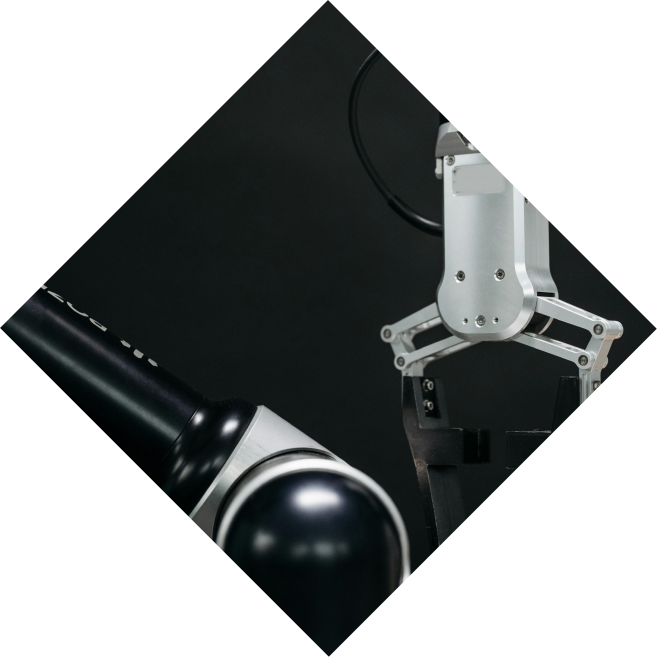